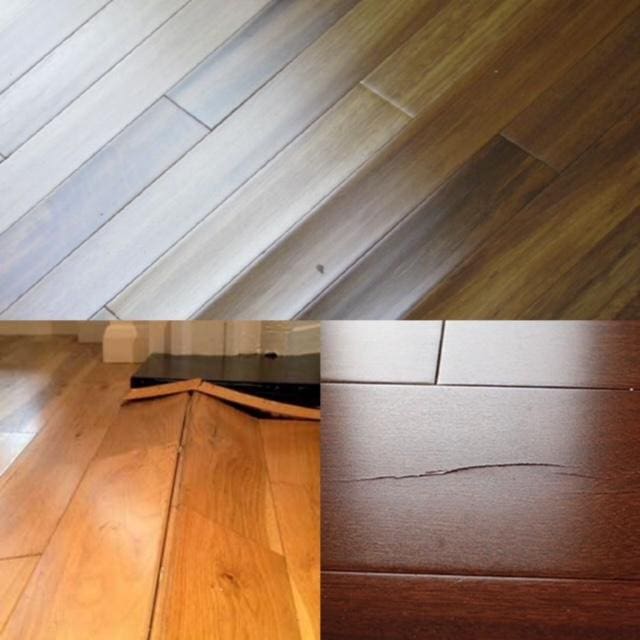
What’s wrong with my hardwood floors?
Do you have a wood floor issue? Here are the most common ones.
Water/Moisture issues account for the majority of problems when it comes to wood flooring! Let’s talk about those and some other issues you may have!
BUCKLING: The wood floor has separated, lifted or “teepeed” from the subfloor.
Causes: Increase in moisture from the HVAC system, wet subfloors from a leaky fridge/dishwasher, poor building drainage resulting in rainwater being directed TO the building, as opposed as away from the building, moisture from poorly ventilated or unconditioned crawlspaces. Other causes include wet-mopping or using steam mops, not maintaining proper relative humidity levels in the home (30-50%), inadequate expansion spacing around the perimeter of the rooms (not allowing the flooring to expand/contract throughout the seasons), improper nailing schedule (not using enough or the wrong length nails).
CUPPING: A concave or dished appearance of individual boards with the edges of the boards raised higher than the center.
Causes: Wood will shrink/swell in relation to its grain orientation. When there is a moisture imbalance through the thickness of the wood, generally cupping occurs, especially when there is a higher concentration of water, at the underside of the wood plank (slow leak from fridge water line or dishwasher are where we see this the most). When wood is installed at a lower moisture content than the in-use conditions allow. The gain in moisture, can often result in the wood swelling and cupping. Wet mopping or using steam mops.
CROWNING: A convex or crowned appearance of individual boards with the center of the board higher than the edges.
Causes: When there is a moisture imbalance throughout the thickness of the wood, with a higher concentration of water at the top or face of the board. We see this most often if there was a leak from a bathroom above, where the water sat on top of the wood flooring for an extended period of time.
DRY CUPPING: A concave of dished appearance of individual ENGINEERED flooring plank, where the edges are raised higher than the center.
Causes: When relative humidity levels remain below the manufacturer’s recommendations for long enough, engineered planks can begin to pull upward, from the substrate of the wood plank, this creates a cupped appearance across the boards. Solid wood flooring can dry cup when it experiences rapid drying of the surface.
CHECKS: A lengthwise separation of the wood cells that normally extend across the rings of annual growth as a result of stresses from the drying process. These look like thin voids (thickness of a few sheets of paper) linear lines on the face of the wood.
Causes: We see this most often in older homes in Cleveland, where the are radiators and no humidity control systems (Aprilaire), causing the wood to dry out over time and create these checks. This can also happen with extreme cycling of very high and very low moisture levels (just like Cleveland’s weather) throughout the house.
SHAKE: A separation of the wood fibers along the grain (parallel to the growth rings) that usually occur between the rings of annual growth. Shake looks like a very thin layer of wood coming up or lifting from the board.
Causes: Gale or hurricane force winds that can wound the tree during its growth, before the tree is harvested for flooring. Damage that can be caused during the felling of a tree. During the finishing process, if water-based finish is used, it can sometimes lift the face of the wood and expose damage, that was previously concealed. Also, changes in the environmental conditions can expose shake.
WOOD DESTROYING INSECTS: An invasion of live wood-destroying insects, which may include powderpost beetles or termites. Almost all wood flooring is kiln dried. Properly kiln dried flooring will kill any insects and larvae in the wood. Small worm holes in the face of the wood, that were present at the installation, often occur and are considered acceptable. Powderpost beetle damage looks like small holes or tunnels in the wood. Termite are attracted to areas in your home where moisture accumulates in and around your home. This damage looks more like a rotting or break down of the wood, exposing more of the layers of the wood.
OVERWOOD/UNDERWOOD: A vertical offset that exists between two adjoining installed floorboards.
Causes: Manufacturing defect during the milling of the flooring.
Characteristic of reclaimed or distressed flooring.
Irregular subfloor, not flat.
Wrong size fasteners used during the installation of the floors.
Debris between the subfloor and the wood floors.
Board replacement done improperly.
WOOD DISCOLORATION: The wood itself changes color over time (darkens or lightens).
Causes: Wood changes color through oxidation and/or photochemical exposure, this can not be prevented.
Some woods (American cherry, Jatoba, Douglas Fir, and purpleheart) darken with age.
Some woods (black walnut and cork) lighten with age.
Areas covered with rugs for an extended period of time, may change color at a slower rate.
A repair area that was not color matched/stained properly.
MINERAL STREAKS/DEPOSITS: A discolored line, spot or band in the wood that may range in color from light gray to tan, olive green, brown, purple, blue or black. Mineral streaks/deposits are naturally occurring and they are often considered to add value and appeal to the wood.
STAINS: The wood or finish changes color due to a variety of factors.
Causes: Rust from the fasteners show up as black/gray stains at or between the boards.
Plant pots from over watering- Anywhere from white to gray to black.
Pet feces or urine- Anywhere from white to black, depending on the damage.
Fungus or mold related- typically gray or black in color.
Moisture from below can cause dark staining or white hazy areas.
Chemical spill- paint thinner, Goof-off, scented plug-in oils, etc can cause many different colored stains.
HOLLOW SOUNDS: An audible hollow sound in the installed wood flooring. If no deflection (vertical up and down movement of the wood) is present, this may be considered normal with many installation methods. Hollow sounds are not a direct concern with an installed wood floor as long as there is not movement accompanying the audible hollow sound. Sometimes glue can be injected into these areas to help quiet the sound.
SQUEEKING/POPPING: Audible sounds in an installed floor or within the floor system. Squeaks are not a direct concern with the installed wood floor as long as movement accompanying the audible squeak does not affect the performance of the installation. An occasional squeak within any properly installed wood floor system is not abnormal.
SEASONAL GAPS: Gaps that appear between individual boards, opening and closing with seasonal humidity changes. Wider boards can experience wider gaps. Gaps size is directly related and proportional to the board width. Most gaps are caused by seasonal fluctuations in relative humidity. Most floors contract with periods of low humidity and expand with periods of high humidity, this is why your gaps are the largest in the winter, especially if you do not have any humidity controls in the home.
Now there are many more issues than these. Feel free to contact us and we would be happy to discuss your particular issues and develop a plan to solve your problem.